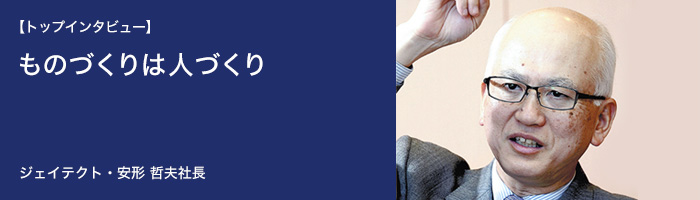
2015年3月17日
ジェイテクトは世界初の電動パワーステアリングを開発した「光洋精工」と、機械部品を加工する工作機械メーカー「豊田工機」が合併して2006年に誕生した。トヨタ自動車が世界に先駆けて発売した燃料電池車「MIRAI(ミライ)」にもジェイテクトの技術が投入され、その技術力は自動車産業をはじめ、鉄道、鉄鋼、重機、風力発電など広範囲に及ぶ。安形哲夫社長(61)は「ものづくりは人づくりです。これからも人材を育成し、我が国のものづくりを縁の下から支えていきたい」と語る。
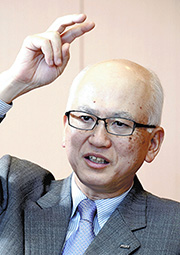
安形 哲夫(あがた・てつお)
1953年愛知県生まれ。一橋大学社会学部卒業後、76年トヨタ自動車工業(現・トヨタ自動車)入社。新車進行管理部長、生産管理部長、専務に就いた後、豊田自動織機副社長を経て、2013年からジェイテクト社長。
——主力製品である電動パワーステアリングはどのようにして生まれたのか。
安形 軽自動車大手のスズキから、車庫入れする時だけ、ハンドルを軽くしてほしいとの要請を受けたのがきっかけです。軽自動車を運転することが多い女性の力でも楽にハンドルが切れないかという要望がありました。実際、大きくハンドルを切るのは車庫入れ、駐車時など、わずかです。ふだんの走行ではハンドルを大きく切る必要はありません。それまでのパワステはエンジンの動力を利用する油圧式で、ハンドルを切っていない時でも常にパワステに動力を伝えており、エンジンに負荷がかかっていました。電動パワステは必要な時だけモーターで補助するので、燃費の向上にもつながりました。
——油圧式に比べ、電動式はハンドルが軽くなった。
安形 いつも軽いわけではありません。真っすぐに走行している時は安定し、大きく切る時は軽くなるよう、操作に応じてコンピューターで制御しています。メーカーや車種によってステアリングに求められる操舵感が異なるので、それに応じたパワステを納入しています。
——軸受けとは。
安形 ベアリング(bearing)といった方が分かりやすいかもしれません。ベアには支えるという意味があり、回転する軸を受けて支えるのが軸受けです。滑らかに動かすと同時に耐久性が求められます。車をはじめ、鉄道、鉄鋼、風力、重機など、「回転するところにベアリングあり」で、広い分野の製品を支えています。
例えば、高速で走行する新幹線。車両の重量を支えながら時速300キロ・メートル近くの速度でも安定して滑らかに走る部品として使われています。製鉄所では1200度の鉄を何度もロールにくぐらせて押し伸ばしますが、そのロールを支える圧延機の軸受けは当社が1943年、国内で初めて開発、量産しました。このように高速、高荷重、高温といった過酷な環境でも高い精度を保ち、滑らかな回転で稼働効率を向上させ、社会の動きを支えるとともに、エネルギー消費の低減に貢献しています。
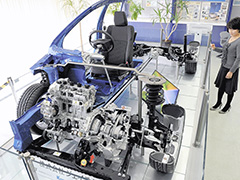
自動車に使われているジェイテクトの製品
——工作機械は。
安形 あらゆる工業製品の部品になる金属を削ったり、研磨したりするのが工作機械です。加工部品を回転させ、刃に当てて削る旋盤、逆に刃を回転させて部品を削るフライス盤。丸いもの、平らなものなど用途に応じて使い分けますが、部品加工には1000分の1ミリという高い精度が求められますので、工作機械の部品の一部は熟練技能者の手作業によって仕上げています。そうした技術によって、20年以上使用しても高い精度を維持する円筒研削盤を生み出しました。
——燃料電池車「ミライ」にも技術投入している。
安形 水素社会をにらみ、この十数年取り組んでいます。燃料を入れる水素タンクは700気圧と高圧です。水素を外に漏らさないよう、極めて気密性の高いバルブを開発しました。当社がこれまで培ってきた精密な技術が生かされたと思います。
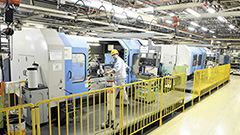
工作機械を製造しているジェイテクト刈谷工場
——ところで、二足歩行型の阿波おどりロボット「すだちくん」は器用に踊る。開発した理由は。
安形 実用化するための研究開発ではなく、技術者の自由な発想を育てることが目的です。動力のモーター、手足の関節には高精度のベアリング、ギアを使い、動きはすべて電子制御です。いつか、何らかの製品を開発する時に役立つかもしれないという考えからです。こうして生まれた技術は、「技術の棚」とでも呼べるファイルに入れて置く。製品開発にあたって、「そういえば、あんな技術があった」と、棚から出してくる。この棚は、いつも更新していきます。
——企業の原点は。
安形 ものづくりは、人づくりです。何よりも人材を育成することが肝要です。当社では1941年に技能者養成所を開設しました。企業内職業訓練校で、技術・技能者としての基礎を身につけ、現場に出てからは、先輩が指導し、技能を継承しています。これまでに従業員は「現代の名工」が20人、黄綬褒章は15人が受章しています。熟練技能者が中心となって現場の技能レベルの維持、向上を担っているのです。
当社が世の中に送り出している製品は各分野の部品として使われ、外から見ることはほとんどできませんが、これからも縁の下で我が国のものづくりを支えていきたいと思っています。
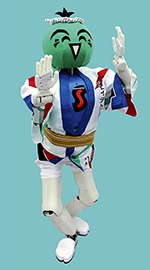
阿波おどりロボット「すだちくん」(ジェイテクト提供)
鉄に命を吹き込む 現代の名工・池田 政義さん
0.01ミリ見逃さず
「0・01ミリは大きなでこぼこです。人間の感覚はとても優れており、熟練してくると、分かるようになります」。ジェイテクト刈谷工場製造技術部改善課の機械工池田政義さん(55)は指先で金属面のひずみを見つけることができる。
中学を卒業すると、豊田工機(現・ジェイテクト)に入社した池田さんは、社内の高等職業訓練校で3年間、基礎的な技能を習得し、機械課に配属された。
携わってきたのは、工作機械に取り付けるオイルボックスのカバー(幅400ミリ、長さ600ミリ、厚さ10ミリ)の薄物金属加工だ。冷却油、潤滑油を入れるカバーは、わずかでもひずみやゆがみがあると、油が染み出てくるため、表面の平坦度を0・01ミリ以内に抑えなければならない。これをフライス盤を駆使して削り上げる。
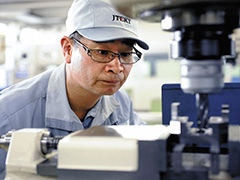
フライス盤を巧みに操る池田さん
フライス盤は、回転する刃(カッター)に加工物を当てて切削する機械で、繊細な感覚が求められる。出来上がると、真っ平らに仕上げられた鋳鉄製の定盤に乗せて平坦度を確認する。
職人技に憧れて入社した池田さんは10年ほどたった頃、先輩から「すごいな。負けたよ」と褒められた。フライス盤で削った後、研磨機で磨き上げて加工は完了するが、池田さんは研磨しなくても済むほどに仕上げたからだ。卓越した技能が認められ、昨年、「現代の名工」に選ばれた。
「鉄の塊を用途に応じて加工する。それが機械の部品になって動き出す。鉄に命を吹き込むのが我々の仕事」
池田さんは先輩から、こう教えられ、今、後輩たちにその心構えを伝える立場でもある。「基礎的な技能を身につけることは必要ですが、熟練していくには『カン・コツ』しかありません」。「勘」と「コツ」であり、「体で覚えるしかない」と言う。
「機械は人の技能がベースになって出来ており、精密なものは、今でも最後は人の手で仕上げます。これからも、この手の感覚を研ぎ澄まし、継承していかなければなりません」
後輩がある日、フライス盤で直角度100分の0・01ミリ以内に仕上げた。「カン・コツ」が引き継がれていることがうれしかった。
ジェイテクト
軸受けメーカー「光洋精工」と工作機械メーカー「豊田工機」が合併して2006年1月に誕生した。1988年に世界で初めて開発した電動パワーステアリングの世界シェア(市場占有率)は25%を占める。自動車部品や新幹線、鉄鋼圧延機用の軸受け、機械部品を加工する工作機械などを製造している。本店は大阪市中央区。同区と名古屋市中村区に本社を置く。